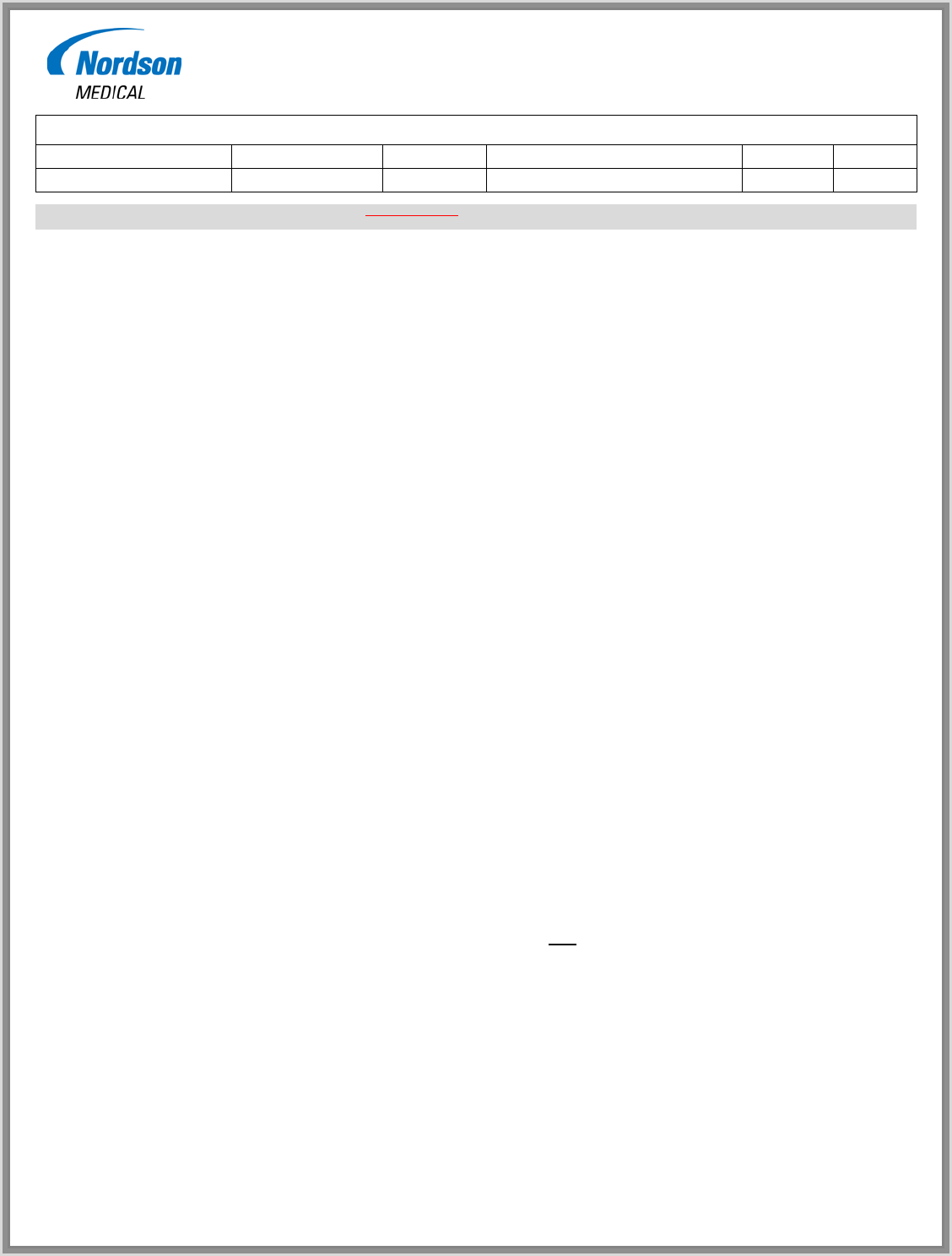
VALIDATION MASTER PLAN FOR VALUE PLASTICS FACILITY MOVE
ANY COPY MADE FROM THE ELECTRONIC VERSION SHALL BE CONSIDERED AN UNCONTROLLED COPY. INDIVIDUALS WITH UNCONTROLLED COPIES ARE RESPONSIBLE FOR ENSURING THE USE OF THE CURRENT
VERSION. REVISION LEVELS ARE ELECTRONICALLY CONTROLLED.
PRINTED HARDCOPIES ARE FOR REFERENCE USE ONLY
1.0 PURPOSE
1.1 The purpose of this Validation Master Plan (VMP) is to identify the validation and testing
requirements necessary to qualify the products manufactured by Value Plastics dba Nordson
MEDICAL after relocation from 3325 South Timberline Road, Ft. Collins, CO 80525 to 805 West
71
st
Street, Loveland, CO 80538.
1.2 There will be no changes to the Quality System, materials, ERP system, tools, equipment,
manufacturing processes and quality inspections as a result of this facility move. In addition the
people who have been doing the work in the current plant will be the same people doing the
work in the new plant.
2.0 POLICY COMPLIANCE
This Plan complies with corporate policy requirements for validation as stated in the Validation
Master Plan IFS document VMP7.1 and ISO 9001 and ISO 13485 requirements
3.0 REVIEWERS, APPROVERS AND EXECUTERS
Reviewers, approvers and executers of this plan are captured in the approval routing tab of this
document in IFS.
4.0 SCOPE OF VALIDATION
NOTE: All products manufactured by Value Plastics are proprietary to Value Plastics; the majority
of the machines, molds and equipment are owned by the company. There is not a 1:1 correlation
with mold and machine for building individual parts (i.e, parts can be built on any number of
machines using a number of different molds). With over 4200 molded parts that can be run in
multiple different machines and molds, it would require over 180,000 individual validations to
verify every possible combination of part and mold to machine. This would result in
approximately 1.42M validation hours. It is not feasible to validate each part in each
configuration. Therefore we will approach this facility move validation in a staged manner. We
will validate every piece of critical manufacturing equipment using a representative mold and part
and will allow our standard quality inspection processes to verify that parts produced post-facility
move continue to meet specification. (Note that we will
conduct a validation for any dedicated
molds/machines.)
This Master Validation Plan addresses all activities related to equipment, utilities, processes, and
systems that may impact product quality post facility move. Specific systems, equipment,
infrastructure and procedures to be qualified and processes to be validated were determined based
on our standard Validation Master Plan (VMP7.1) and associated work instructions.
4.1 In-Scope
4.1.1 Injection Molding Machines moved to new facility
4.1.2 Injection Molding Machine monitoring software
4.1.3 Injection Mold Tooling moved to new facility