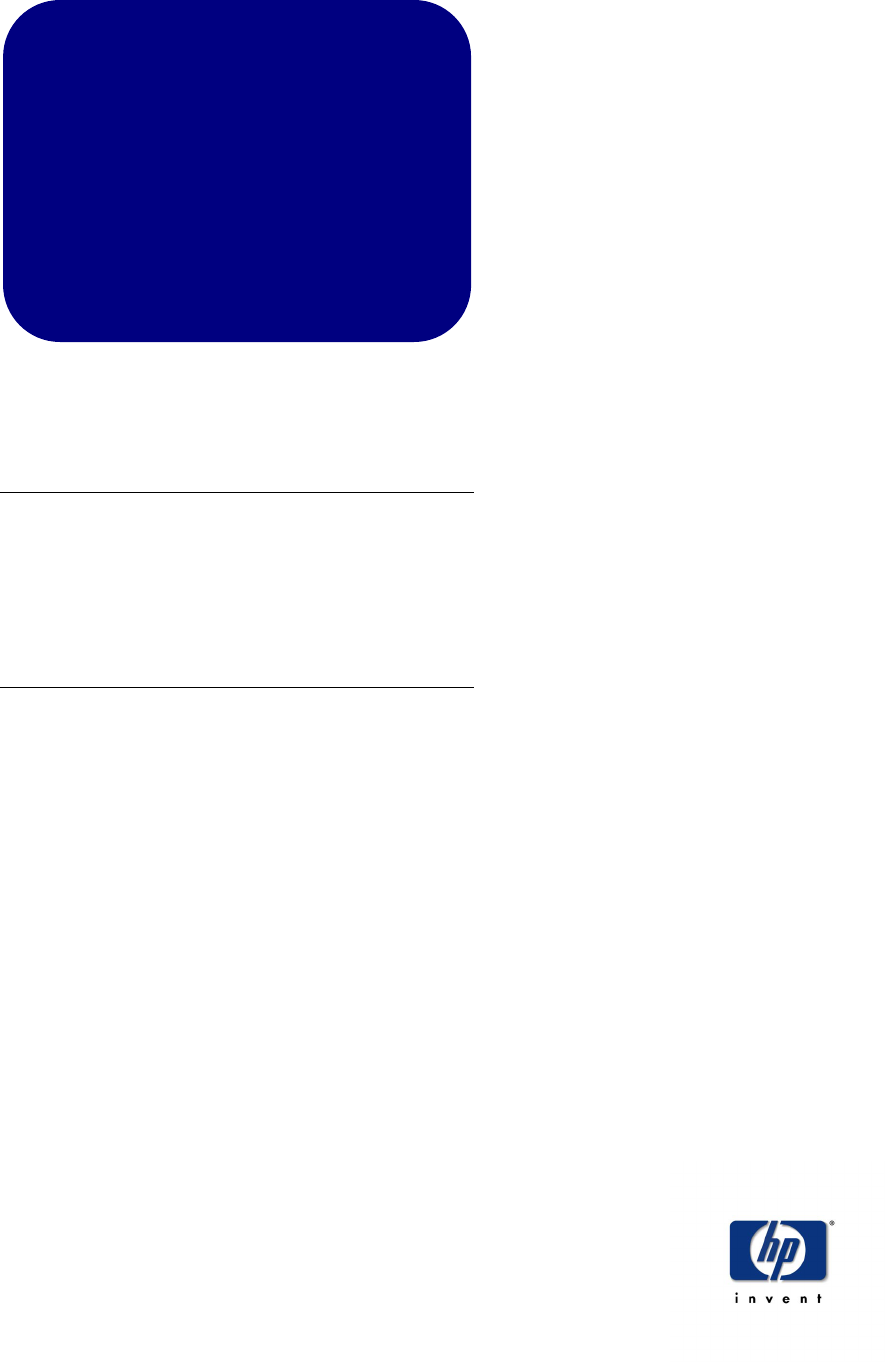
HPL/STL/DTD 2/5/2002
Helping business planners
understand and resolve the
product end-of-lifecycle dilemma
C
CC
Companies that manufacture short-lifecycle products such
as personal computers, mobile telephones, and consumer
electronics are often faced with the product end-of-lifecycle
dilemma:
Should I build out my existing stock of components for soon-
to-be discontinued products, generating finished goods
inventory that may be sold at a reduced price?
Or should I merely scrap or sell at steep discount the
inventory of components and assemblies that are unique to
an end-of-life product?
Or should I do some combination of the two?
The build-out option is further complicated because it often
requires the purchase of additional materials and parts,
increasing the cost of a potentially risky choice. But
“throwing away money” by scrapping obsolete product
components is not a pleasant choice for planners either.
This end-of-lifecycle dilemma is an expensive proposition for
many companies. In highly competitive businesses with low
margins, the costs associated with product rollover and the
resulting management decisions can often mean the
difference between profit and loss.
Hewlett-Packard Laboratories, HP’s research organization,
has developed the Inventory Optimization for Product
Rollover (IOP) tool that allows product planners to analyze
various trade-offs and scenarios for the product end-of-
lifecycle dilemma. HP Consulting has created the IOP
Service by combining the IOP tool with HP’s manufacturing
expertise to deliver a unique and valuable supply chain
planning solution to HP’s clients.
Using proven mathematical optimization technology, the
IOP tool quickly evaluates the countless build/scrap
combinations and helps planners weigh various financial
and business options. HP’s manufacturing consultants work
with clients to tailor the IOP service and ensure that results
meet expectations.
IOP uses business and manufacturing information such as
component and assembly stock on hand, finished product
inventories, component and product costs, and product
demand forecasts. This information is analyzed by the IOP
tool, resulting in decision recommendations about quantities
of products to sell, how much of certain products or
components to build, quantities of additional raw materials
to purchase, and how much of specific parts to scrap or sell
at discount. Product planners are encouraged to use the
IOP tool in an ad hoc mode, performing what-if analysis on
various rollover scenarios and trade-offs. IOP helps
determine the right build-to-stock quantities of products for
various demand forecast assumptions. The ultimate goal is
to give planners the insight and understanding to
confidently make the right set of manufacturing and
business decisions.
Hewlett-Packard has proven the IOP tool approach in
several of its computer product lines. In short lifecycle
products with significant variation in forecast demand and
large write-off costs, using the IOP tool has become a
critical business process at HP. One division of HP that
produces compute servers had annual write-off expenses in
excess of $20 million, a significant fraction of overall profit.
The product planners used IOP to substantially reduce these
end-of-lifecycle write-off costs.
C
CC
Customer demand for new products, agile competitors
spawned by the global market, and advances in
manufacturing technologies are all increasing the effect of
the product end-of-lifecycle dilemma, forcing companies to
incur the cost and management attention involved in
product rollovers. HP’s IOP Service helps solve this
problem, offering a method for turning a previously
expensive and time-consuming business process into a
competitive advantage.
Inventory Optimization
for Product Rollover